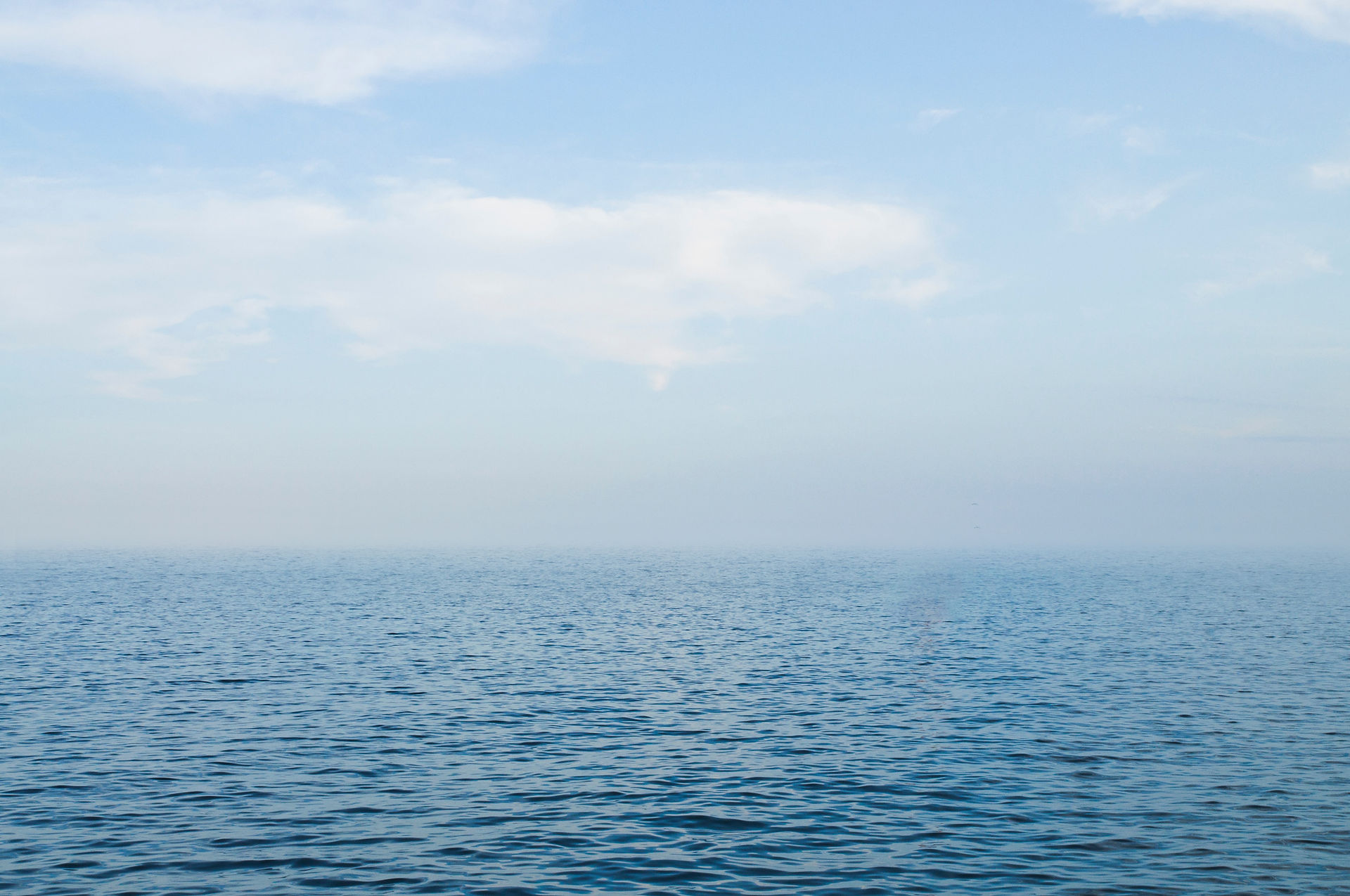
MST
PROPRIETARY DESIGN
CALLED
FORGED TUBULAR JOINTS (FTJ)

FTJ offers improvements in weld joints in many wind turbine foundation systems including:
-
Three-legged and four-legged jackets
-
Semi-submersible
-
Articulated multi-spar
-
Tension-leg platform
FTJs CAN BE SUPPLIED IN A WIDE RANGE OF NODE CONFIGURATIONS USED IN WIND POWER STRUCTURES
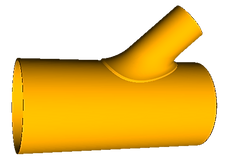

​KEY ADVANTAGES
​​
-
Only pipe-to-pipe girth welds.
-
Simple circumferential weld
joint: 90-degree butt-weld for
all node-to-pipe joints.
-
Semi-automatic welding possible; no manual welding needed.
-
Fewer welding procedures and qualifications needed.
-
Improved geometry provides lower stresses at the joint.
-
Drastically lower weld fatigue.
-
Longer service life due to
enhanced fatigue resistance.
-
Easier weld inspection over
the service life.
-
Possible reduction in branch
diameter and total weight of the structure.


INTEGRATING OUR SUPERIOR
K, Y, & X NODES
IN YOUR SUPPORT STRUCTURE DESIGN CAN ENABLE IMPORTANT IMPROVEMENTS FOR THE ENTIRE STRUCTURE.
LOWER TOTAL STRUCTURE WEIGHT
LONGER
SERVICE LIFE OF SUPPORT STRUCTURE
Depending on the specific project design, steel support structures make up to 35% of total CAPEX
LOWER COST OF MANUFACTURING THE ENTIRE SUPPORT STRUCTURE
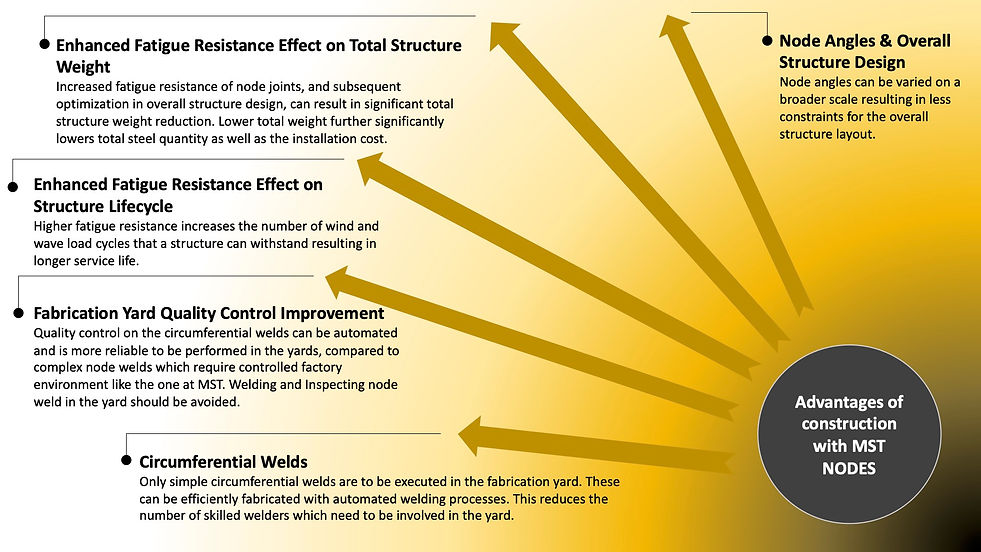
HOW DO WE MAKE THAT POSSIBLE?
We developed next generation wind turbine structure NODES
We reduced Stress Concentration Factors on average between 43-62% depending on the type of node.